AI ENHANCED INSPECTION VS TRADITIONAL
- Aspect
- Defect Detection
- Accessibility
- Efficiency & Cost
- Data Quality
- Digital Integration
-
- AI-assisted analysis with manual verification ensures precise and comprehensive issue identification.
- UAVs can easily reach various parts of a bridge, supported by digital twin simulation for full inspection coverage.
- Low learning and operating costs, easy to use, and highly efficient—single-person operation supported.
- Captures high-resolution images and sub-millimeter-level measurements using professional cameras and positioning tech.
- Digital twin integration enables 3D analysis and centralized defect management for data-driven maintenance decisions.
- Manual inspections are affected by varying skills and responsibility levels, leading to misjudgments and missed defects.
- High piers and complex bridge components are hard to reach, resulting in blind spots.
- Inspection vehicles are expensive, inefficient, and pose operational safety concerns.
- Traditional methods lack complete, high-resolution, and precise data collection.
- Inspection results are hard to visualize, verify, or integrate into management systems.
OUR DRONE BRIDGE INSPECTION WORKFLOW
1. Digital Twin Modeling: Building a Precise 3D Bridge Replica
We start by constructing a high-precision 3D digital twin model of your bridge. This model isn't just a virtual copy; it serves as the visual management foundation for all inspection data and defect information, laying the groundwork for subsequent intelligent flight planning.
Real-world testing has shown that using Riebo's R-series cameras in conjunction with AeroMapPro for bridge 3D modeling, the entire modeling task for a 500-meter bridge, from data acquisition to model generation, takes less than two hours.
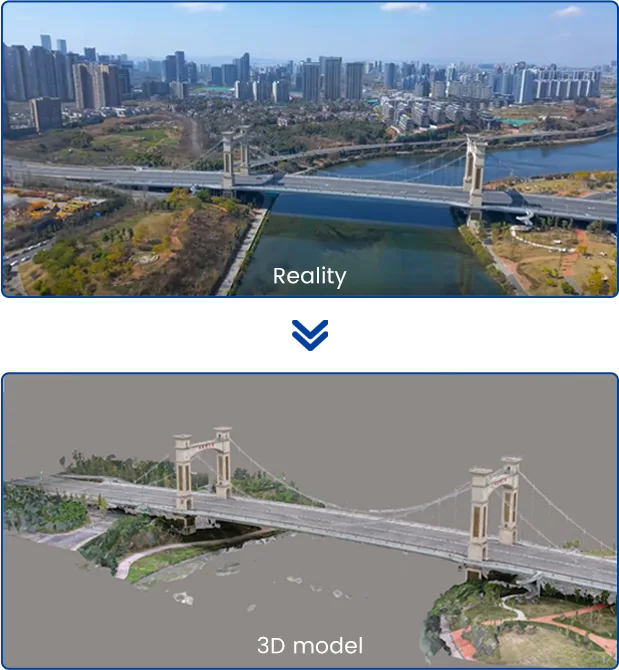
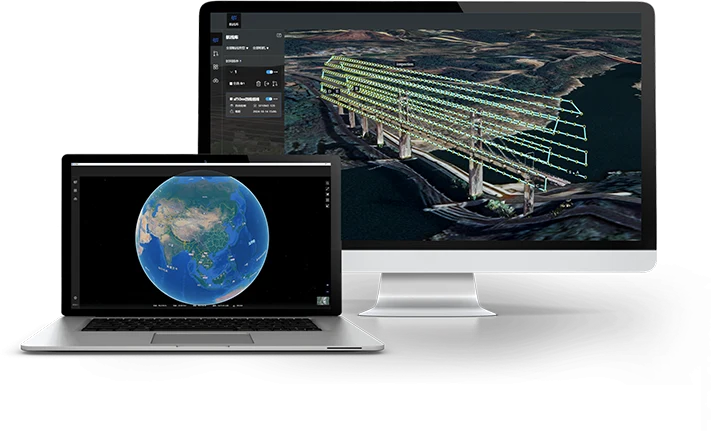
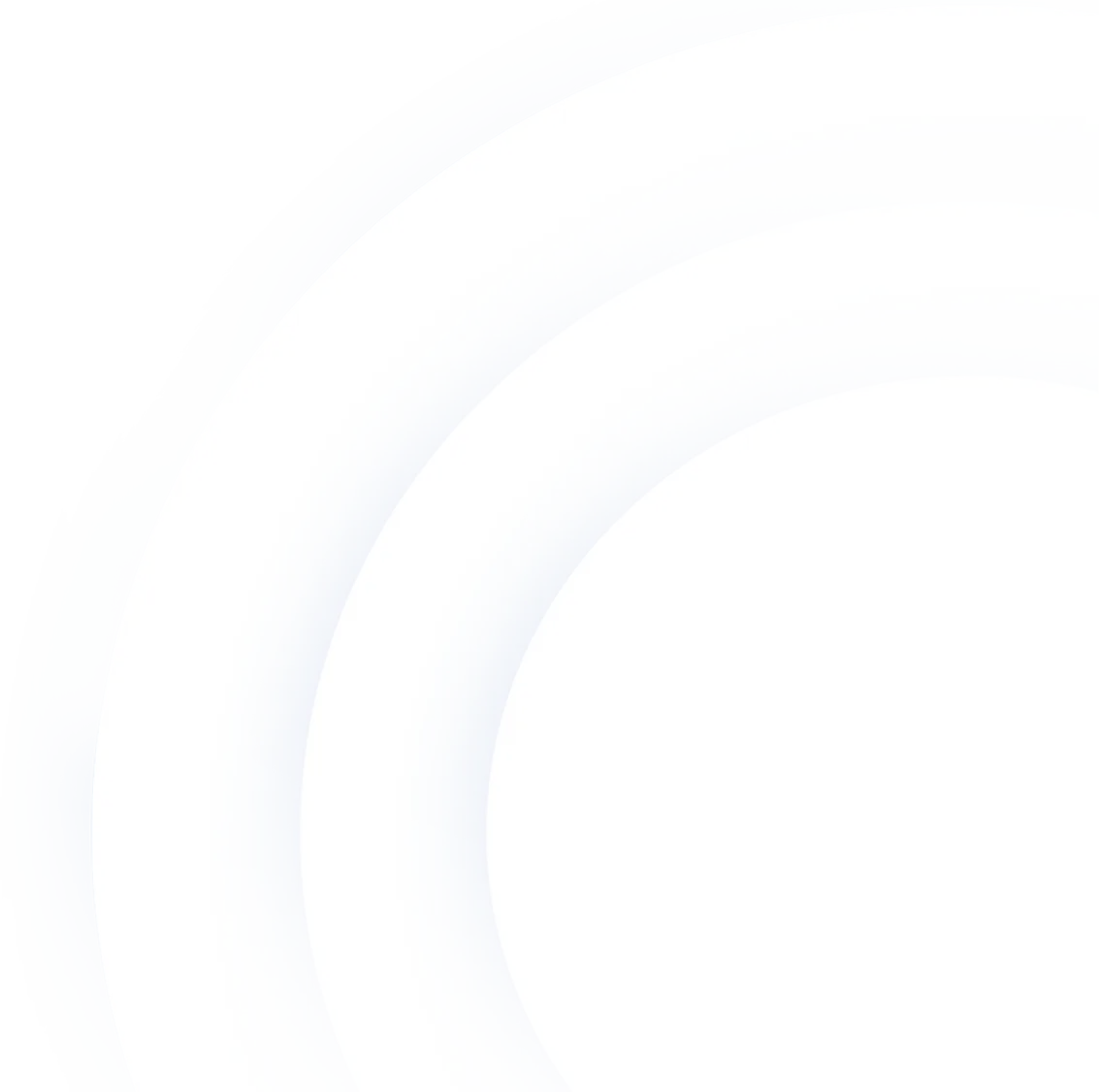
2. Smart Route Planning: Ensuring Comprehensive Coverage & Ultimate Precision
Using the digital twin model, AeroMapPro can automatically generate safe and efficient drone flight routes. These routes are meticulously optimized to ensure comprehensive coverage of all critical bridge structural points, ensuring no subtle crack or damage goes undetected.
In addition, AeroMapPro not only supports automatic route generation but also enables users to dynamically adjust various parameters during operation, significantly improving the efficiency of flight path planning.
3. Efficient Data Capture: Capturing High-Definition Imagery
The acquisition of inspection image data is carried out by DJI M350 RTK equipped with the professional inspection camera SF10. Field operations can be completed with just one person, one vehicle, and a single set of acquisition equipment. They efficiently collect vast amounts of high-resolution image data under the guidance of our optimized flight plans.
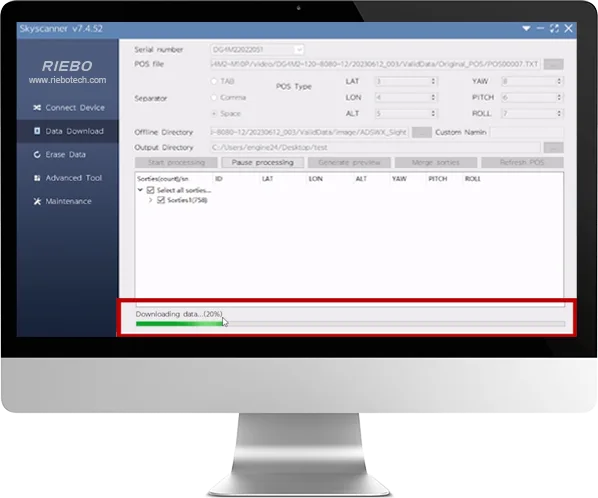
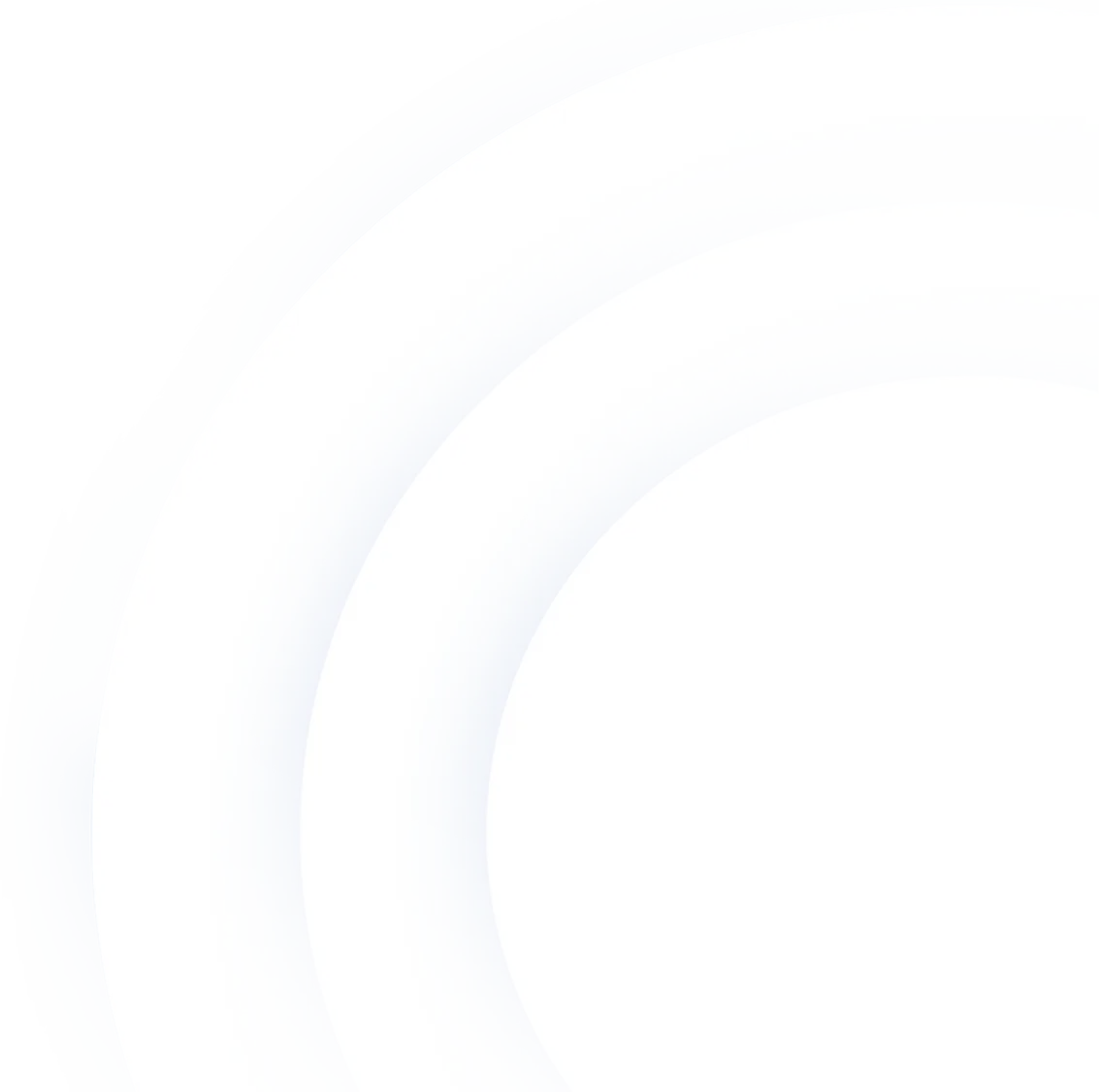
4. SkyScanner Data Processing: Smart Handling of Massive Data
Our SkyScanner software stitches all those images together and adds precise location info. It calculates each photo’s field of view, making sure the data is accurate and ready for the next AI analysis.
5. AI Intelligent Identification: Pinpointing Every Defect Fast
Using advanced AI, we quickly analyze the images to spot and classify defects like cracks, corrosion, or loose bolts. This speeds up inspections and boosts accuracy, catching issues that might be missed by the naked eye.
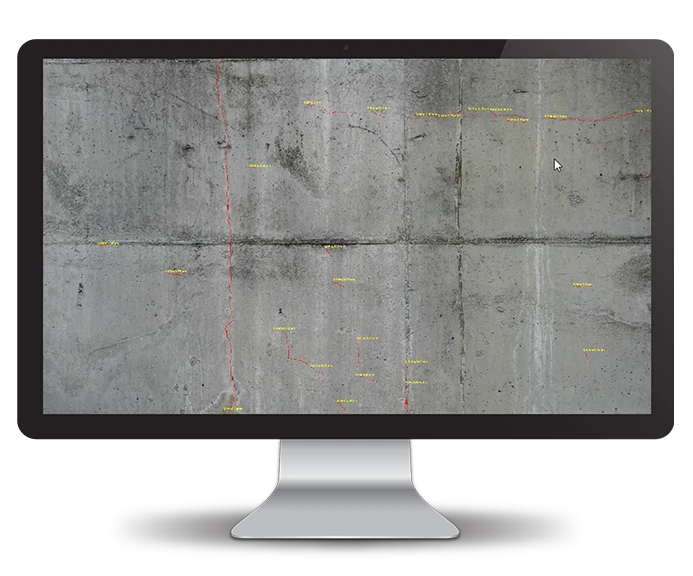
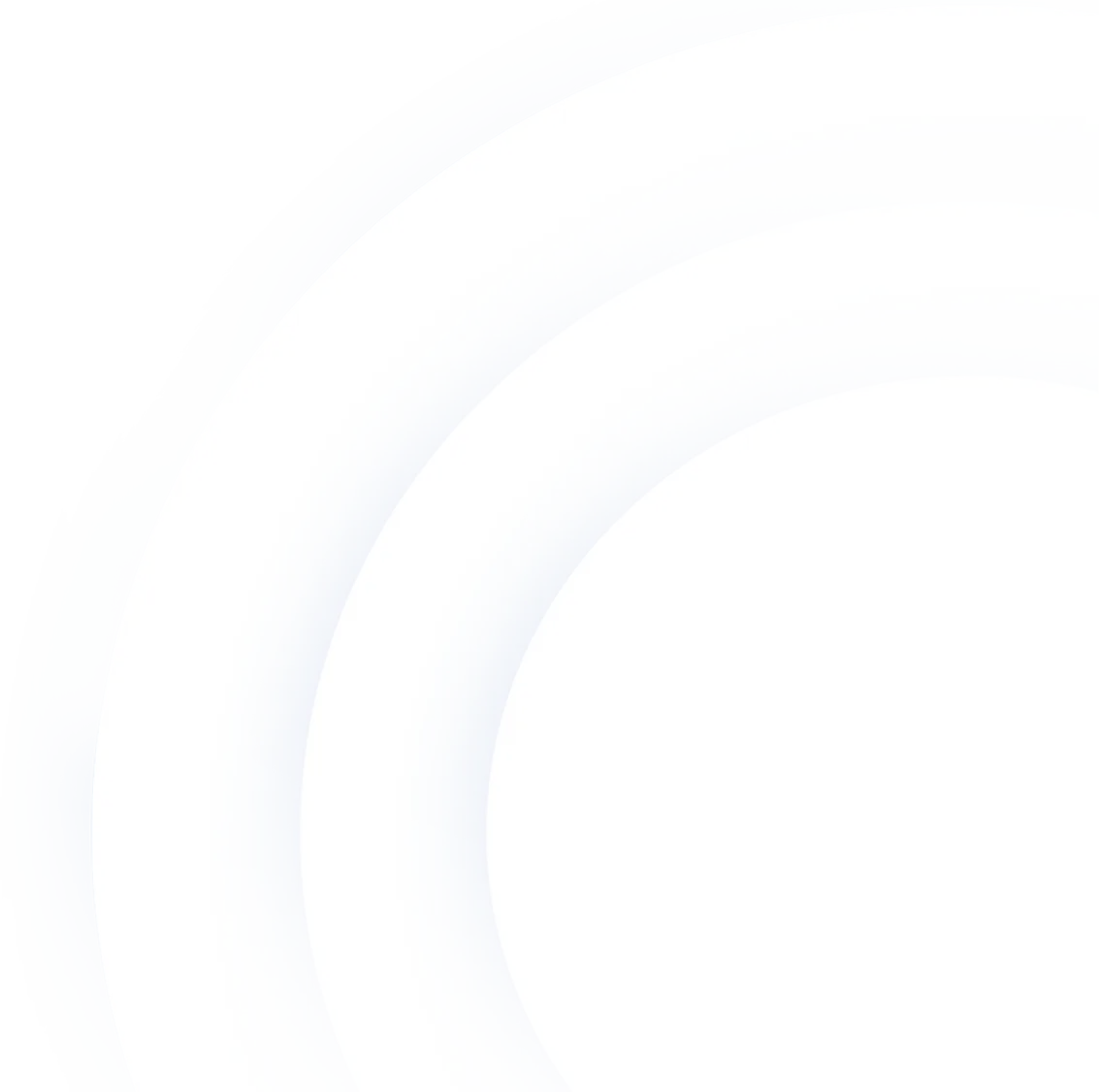
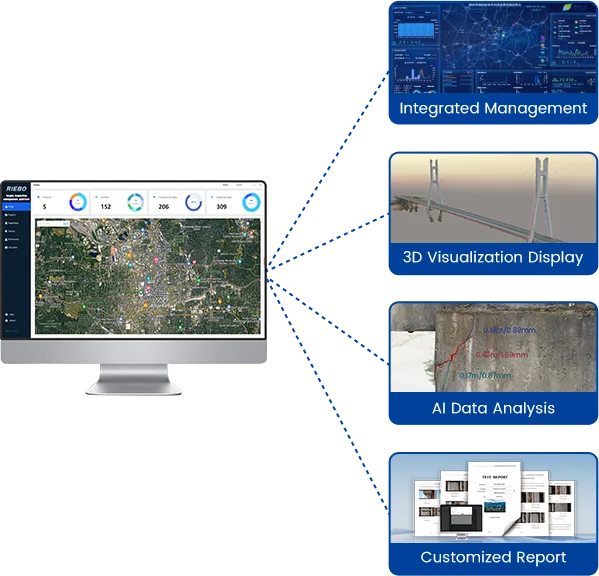
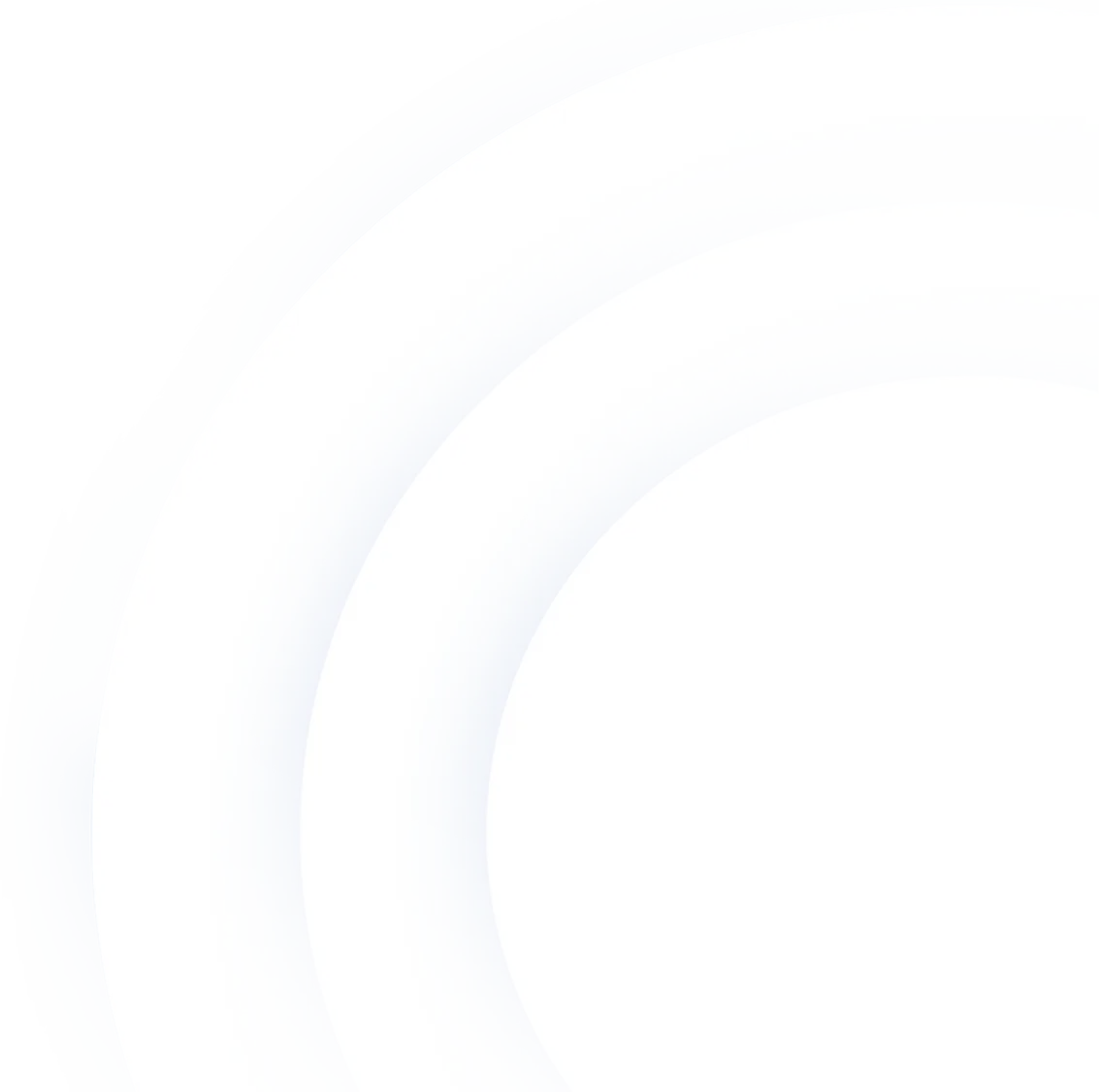
6. RIEBO TongTu Inspection Management Platform: Your Digital Management Hub for Bridge Inspections
Think of this as the brain of your bridge inspection. It brings together all data—from raw images and AI findings to past reports—on one easy-to-use 3D platform. Here you can:
-
Visually Locate Defects: Directly annotate and view defect locations on the 3D model.
-
In-depth Data Mining:Conduct historical data comparison and analysis to understand bridge health trends.
-
Efficient Team Collaboration:Empower cross-departmental collaborative management and simplify report generation.
-
Smart Report Generation:Automatically generate inspection reports compliant with industry standards.
Components of Our System
Data Acquisition System
- High performance drones: We deploy advanced drones such as the DJI M350 RTK, engineered to deliver stable, reliable flight performance even in challenging bridge environments—ensuring consistent operation amid structural obstacles, wind, or confined spaces.
- Inertial Navigation System: Integrated INS technology mitigates the impact of weak GNSS signals in areas like bridge undersides, maintaining precise positioning and trajectory control for uninterrupted data capture. Futher reading: Inertial navigation system
- Pro-Grade Cameras: Equipped with professional-grade payloads including R10Pros photogrammetry camera for centimeter-level 3D modeling, and SF10 inspection camera with LiDAR for rapid, precise focus, the system captures high-quality images capable of detecting 0.1mm cracks and subtle defects like spalling, corrosion, and deformation.
- Smart Flight Planning Software: Our proprietary AeroMapPro flight planning software ensures every mission to be carefully planned to capture complete, high-quality data with maximum efficiency.
- Data Pre-processing Tool: Data processing is carried out using SkyScanner, this software can efficiently manage large inspection datasets, supports batch export, embeds geolocation, and calculates image field of view to enable accurate defect localization by subsequent processes.
Intelligent Management System
To tackle common issues in traditional bridge inspections—like unclear results, messy workflows, and wasted data—Riebo developed the Tongtu Intelligent Inspection Management System. Key features include:
- End-to-End Management: From scheduling and data collection to defect detection and location analysis, everything’s streamlined in one system.
- 3D Visualization: See the bridge and its defects clearly through a digital twin model.
- Smart Data Analysis: Track defect history, predict trends, and dig deep into inspection data.
- Automated Reports: Instantly generate professional reports that meet industry standards.
TYPES OF BRIDGES WE INSPECT
-
Highway BridgesThese high-traffic structures require regular inspection to ensure structural integrity and safety. Drones can efficiently scan underdeck areas and hard-to-reach joints without traffic disruption.
-
Railway BridgesRail bridges demand high-precision inspection due to vibration, load impact, and remote locations. UAVs enable close-range imaging without the need for track shutdown.
-
Cable-Stayed & Suspension BridgesLarge-scale cable structures are complex and difficult to access manually. Drones provide aerial views of cables, towers, and deck elements for stress analysis and damage detection.
FAQs About Bridge Inspection with Drones
-
How does the camera ensure precise focusing?Our camera uses laser rangefinder autofocus, which measures target distance in real time and accurately adjusts the lens to ensure sharp focus under varying distances and lighting conditions.
-
What is the smallest crack it can detect?The minimum focusing distance is 2 meters, enabling image capture with a resolution of 0.05 mm.
-
What weather conditions are suitable for operation?Drone inspection should be conducted in favorable weather—no rain or snow, low wind speeds, adequate lighting, good visibility, and moderate temperatures—to ensure flight safety and data quality.
-
Can the underside of a bridge be used for 3D modeling?Yes. With our high-resolution camera, autonomous navigation technology, and specialized flight planning software, high-quality images can be captured even under bridges where lighting is low and GPS signals are weak—meeting the requirements for accurate 3D reconstruction.
-
Can the camera capture clear images in poorly lit areas inside a bridge?Yes. Our camera is equipped with an automatic auxiliary lighting system, enabling proper exposure at a distance of 6 meters even at night.